Furniture Making - Joints Week - Make a Table, all you need to know about joints
Description
Time to make your first piece of furniture! Or, perhaps, time to make your first accurate, crisp, precisely-made, piece of furniture. This is a great follow-on course from ‘Skills Week’ but will also happily stand alone if you have at least a little woodworking experience. Successful furniture making is based on good design, well thought out construction, and accurate execution of all the many components and joints that will be brought together to create, not just an elegant piece of furniture, but an elegant piece of furniture that doesn’t fall apart or try to self-destruct. We often talk about a ‘Zen-like mind-set’ that’s required to saw perfect dovetails, but we also need to acquire a constant ‘Cabinet-Maker’s mind-set’, which is all about control, and using well thought out sequencing. A precise process requires a meticulous mind-set. ‘Making it up as you go along’ is not impossible when making furniture – a new design usually needs to be tweaked or re-thought here and there, but in general, ‘If you fail to plan,……………!’ So, with all this in mind, we’ll start by looking at the thought-process and considerations that were made during the design of this table to give it a crisp, contemporary styling and look at how, and why, the variety of modern and traditional joints were selected. I have been known to bang-on a bit about sharpening, not because I have a disturbing obsession with shiny, razor-sharp pieces of metal, but because without sharp tools you might as well not bother with woodwork. So, we’ll spend a little time on a recap of the sharpening process, but don’t panic, you’ll be provided with a full set of sharp tools to get you started. It’s vital that you keep track of which bit goes where when making even the smallest, simplest project. I embraced the ‘Triangle System’ a few years ago when I was teaching in Germany, so I’ll pass on this wonderfully simple method of keeping all of the twenty-odd table components facing in the right direction. Your kit of components will need just a little work from you to get them crisp and square and to the finished size, but we will be focussing much more on understanding the cabinetmaking process and the accurate cutting of joints, and much less on endless, blister-inducing, hand-planing, which might just put you off the whole idea of working with wood. This course will give you the opportunity to cut some elegant, traditional joints completely by hand but will also give you the chance to use a couple of the most-used power tools in any professional workshop, the ‘Biscuit Jointer’ and the ‘Domino’. Mitres are notoriously tricky joints to cut accurately, but, at the same time, are an incredibly slick way of getting round corners (if you get them right!). Renowned for giving you absolutely nowhere to hide with even the slightest of mistakes, we have a cunning plan for getting the mitred lipping around the veneered table-top spot on every time. Add to this some strategies for the stress-free gluing of all your lovingly hand-crafted components and you will have come a long way towards becoming a controlled, confident, competent cabinet-maker. This table making project will include drawer rails and runners and a drawer-front, but the making of the drawer itself, forms the basis of a separate Dovetailing & Drawer-making course.)What will you learn: * Sharpening – a quick recap of the method we use to produce razor-sharp blades * Desin – The process of design including: Joint selection; Coping with wood movement and Structural stability * Marking Out – the annoyingly clever Continental method of keeping components under control * Modern joint cutting power tools – setting up and using the biscuit jointer and Domino mitres – a fool-proof method for cutting this very challenging joint * Essential hand cut joints – hand cutting two elegant, timeless joints – the mortice & tenon and the dovetail (Bare-faced stub mortice & tenon and lapped dovetail, if you want to get technical) * Using a finesse tool – A spokeshave will be used to cut some curves at the tops of the leg chamfers and on the drawer rail to facilitate future drawer opening. * Gluing - This is where there’s huge potential for getting into a horrible sticky mess and spoiling all those hours of work that have led up to this point. We will look at glue choice and some simple, reliable strategies for stress-free glue–ups.
Duration
5 weeks
Cancellation policy
Non-refundable - Refunds are not available
Maker
Over the 35 years I have been running a successful bespoke furniture making and antique restoration business, I have become passionate about passing on the skills and knowledge through my Woodworking School. We have designed a range of educational long and short courses that have traditional hand skills at their core, the key requirement being simply enthusiasm and a thirst for knowledge.
Suitable for
- Adults
- Daytime (weekdays)
- Intermediate level
- Parking provided
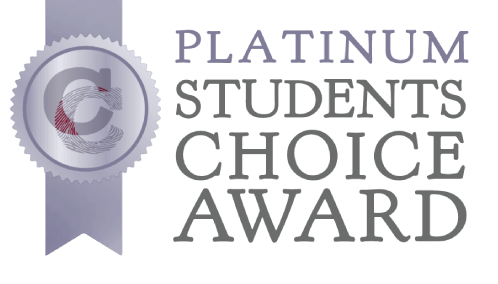
FAQs
Teaching is from 9am until 6pm each day except the final day when the course ends at 5pm to allow for those with long journeys home.
Venue
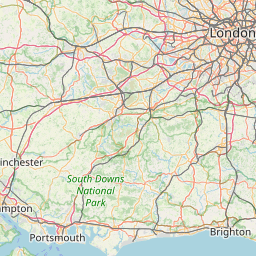
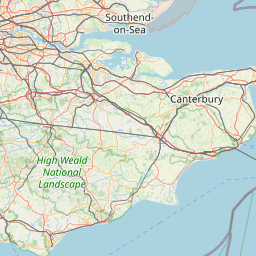
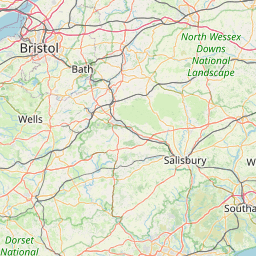
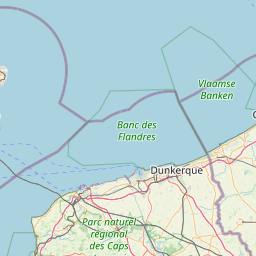
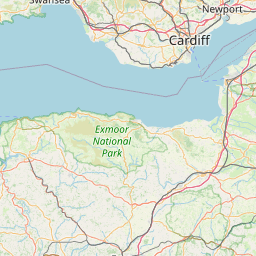
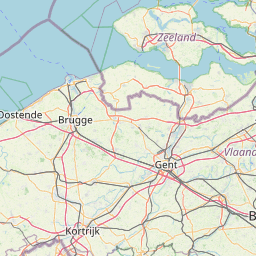
