Description
If you have any sort of urge to move on from straight lines and get a few curves into your woodworking designs, laminating is going to be the vital technique that you will need to master. In essence, laminating is a pretty simple concept, after all it’s just combining thin bits of wood with glue, and holding them in the desired shape until the glue has set. As with most simple things though, there are tricks and techniques that will give you a head start and guarantee success. MOULDS & LAMINATES: Moulds for curved work can be made in many different ways and after many years of creating curvaceous pieces of furniture we have quick and fool-proof solutions for ‘in-house’ mould making. What should you use for your laminates? Constructional veneer, flexible plywood, laminates cut from the solid on a band-saw? It’s important that you get the choice of material correct, this will vary depending on what you’re making, a door, a drawer front, a box lid...so we’ll look at the options and the pros and cons, so that you can make an informed choice about what’s most appropriate for a particular project. EQUIPMENT: Inevitably there are some specialist tools and pieces of equipment that will make the process of laminating easier, and we will look at low tech solutions which might involve lots of MDF and many cramps. Every time I use a vacuum press, I think it must surely be something to do with the dark arts, it’s certainly as close as any woodworker’s going to get to a magic trick. This is an incredibly simple system and perfect for the small workshop, no need for huge hydraulic presses, just a small box of bits a bag and a pump. You’ll be amazed at what a vacuum press can do, it can certainly be a real game changer, we’ll look at how to set up and use this amazing piece of kit for creating curves and look at the other things it can do for you. We’ll also look at some other systems for persuading flat things to become a little more voluptuous. GLUES: Laminating is all about sticking things together so it’s vital that you pick the right glue. Different glues have different properties, we’ll look at the glues that are available at the moment, some old favourites and some new innovations. Which are the best behaved glues for laminating work? We’ll also look at all the technical stuff like shelf-life, open-times, press times, mixing ratios, solvents. Just choosing the right glue can be the difference between a pleasant, successful experience and a nasty sticky nightmare. Surprises can often be nice things, but when making laminated components, reliable predictability is really what we need. BOX PROJECT: Having made friends with the various processes, creating a curvaceous test piece which might become a ‘banana stand’, it will be time to try out your new skills by making a small box. This project will be a chance to practice some woodworking skills too; preparing some nice, accurate, flat components, there will be techniques and jigs, including a ‘Donkey’s Ear’, for cutting crisp mitre joints by hand, letting in some hinges and, of course, laminating, veneering and fitting the curved lid. What you will Learn: LAMINATES – How to choose laminate materials for a particular project GLUES – Types, properties, solvents. MOULDS – Types, materials and techniques for accurate home-made moulds. EQUIPMENT – Tools, cramps, routers… used for making moulds and laminating. VACUUM PRESS – Options, types, bags; tried and tested methods for using this cunning piece of equipment in a smaller workshop. VENEERING – Adding veneer to a curved surface using a vacuum press. CABINETMAKING SKILLS – Accurately preparing components, hand-cutting mitres, using shooting boards and jigs, cutting grooves with a router table, letting in and fitting hinges
What's included in the price?
All tools and materials. Safety equipment if required. Refreshment breaks with tea, coffee, biscuits, and cakes.
Duration
3 days
Cancellation policy
Non-refundable - Refunds are not available
Maker
Over the 35 years I have been running a successful bespoke furniture making and antique restoration business, I have become passionate about passing on the skills and knowledge through my Woodworking School. We have designed a range of educational long and short courses that have traditional hand skills at their core, the key requirement being simply enthusiasm and a thirst for knowledge.
FAQs
Teaching is from 9am until 6pm each day except the final day when the course ends at 5pm to allow for those with long journeys home.
Venue
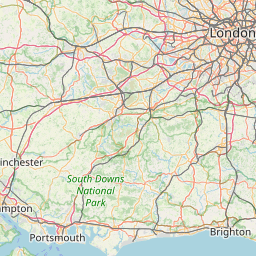
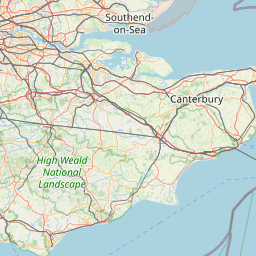
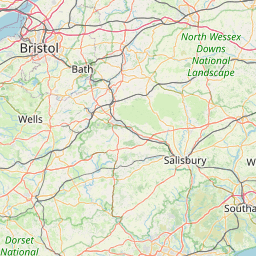
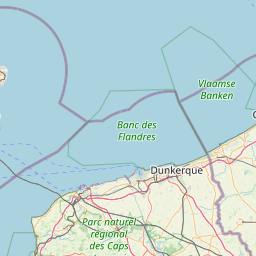
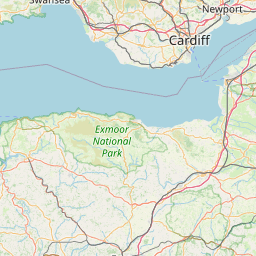
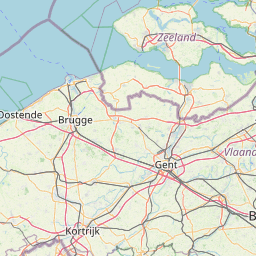
